Collaborative Robots: The Role Of Robotics In Industry
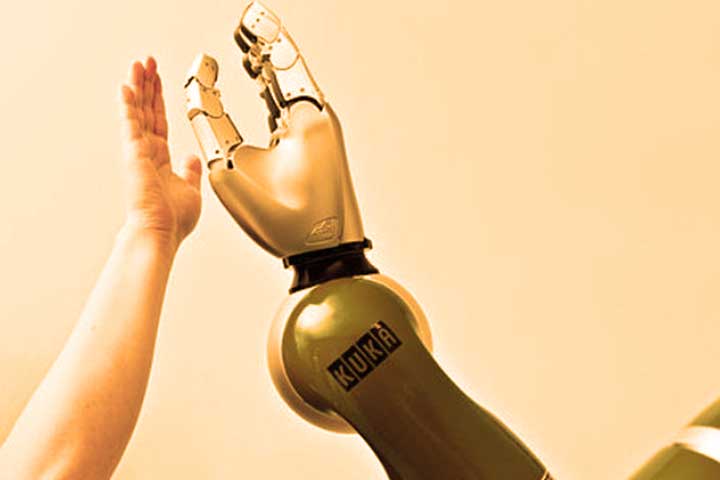
Collaborative robots are a reasonably new concept in our usual vocabulary, but in the industry, it is an element that rings quite strongly.
And the world of technology is advancing by leaps and bounds. For this reason, the industries are always fully updated to apply the best advances in the sector that make the production process more efficient.
Thus, the futuristic idea of humans working closely with robots is already a reality, even in areas we could not even imagine.
Advantages of robots in the industry
Within Industry 4.0, robots play a very important role thanks to all the advantages they provide:
- They ensure a high level of productivity and dialogue since they use different protocols and elements that make communication with the machine control faster and safer.
- They offer greater precision in high repeatability applications, which leads to a reduction in operating errors that allows for improving the quality ratios in all its movements. This has a positive effect, above all, on pick & place and inspection applications. Thus, energy savings are more significant, the consumption of raw materials is reduced, and the return on investment is created in a shorter period.
Artificial intelligence, where robotics seeks to imitate a human, both emotionally and physically (movement), has made it possible to change the concept of the conventional robot.
Today it is possible to apply robotic technology in other industries such as medical surgery, transportation, physical rehabilitation of people, intelligent prosthetics, or underwater inspections, among others.
There are many benefits that robotics brings to our daily lives. Therefore, in the future, this technology should allow us to have a better quality of life, whether in a factory or at home.
All these possibilities are made real thanks, as we have anticipated, to a new technological concept that is going strong in the industry: collaborative robots.
People will still run the future factories, but collaborative robots will power them. Integrating this technology implies a change in the production lines by making them more efficient in collaboration with the operator. Thanks to this, the range of application possibilities and sectors of use is immense and allows the automation of any process.
Collaborative robots
Why build a collaborative robot?
The installation in a factory of a collaborative robot is much faster than that of a conventional robot since it does not need fences and safety equipment, such as barriers or scanners.
But, in addition to all these advantages for its implementation, it offers many more functional benefits that make collaborative robotics the best option for today’s industries :
- Easy and fast programming and configuration of the robot.
- Specialized technicians are not required for its assembly and operation.
- You can work safely with one operator.
- It is the best solution in companies where you want to optimize processes and reduce possible risks associated with the health of operators.
- Reliability in operations where zero operator failure is sought with the consequent reduction in material cost and machine downtime.
- Faster cycle times.
- It makes robotics more affordable for small and medium-sized companies by improving their production processes.
All the major manufacturers of conventional robotics have developed collaborative robotics. So much so that, at present, there are exclusive manufacturers of collaborative robotics.
The importance of this type of technology is so great that today there are robots with up to 6 and 7 axes or even a humanoid appearance. Collaborative clamps or arms have also been created.
Thanks to the existing ambition in the industry and its continuous search for excellence in all processes and cost savings, collaborative robotics tends towards unstoppable growth.
Also Read: What Is RPA (Robotic Process Automation)?